What to Get out of a Comprehensive Welding Inspection Racine
Wiki Article
Cutting-edge Approaches to Fillet Weld Examination and Screening: Enhancing Weld Top Quality and Conformity Standards
In the realm of welding, the high quality and integrity of fillet welds play an essential function in ensuring the architectural sturdiness and integrity of numerous industrial parts. With the continuous drive for improved performance and compliance with strict requirements, the exploration of ingenious strategies to fillet weld evaluation and testing has come to be vital.
Advanced Non-Destructive Testing Methods
Making use of modern innovations, progressed non-destructive testing methods play a critical function in making certain the honesty and top quality of fillet welds. These techniques, such as phased variety ultrasonic screening (PAUT) and magnetic fragment screening (MPT), offer detailed understandings right into the weld's internal structure without causing any kind of damages to the product. PAUT, as an example, makes use of multiple ultrasonic elements to evaluate the weld from numerous angles, supplying a thorough visualization of possible flaws like lack of combination or splits.By utilizing these sophisticated non-destructive screening methods, weld examiners can precisely examine the high quality of fillet welds, ensuring compliance with sector criteria and policies. The capability to detect defects early on not just boosts weld quality but likewise avoids expensive rework or failings in architectural integrity, highlighting the significance of these innovative testing methods in welding assessments.
Robotics and Automation in Assessment
The assimilation of robotics and automation has actually revolutionized the assessment process for fillet welds, boosting performance and accuracy in quality evaluation. Robotics use accurate control and repeatability in examining welds, making certain dependable and regular outcomes. Automated systems can be configured to follow details inspection paths, making sure thorough insurance coverage of welds and minimizing the threat of human error.Robotic inspection systems outfitted with innovative sensors can spot and determine weld features with high precision, providing detailed data for analysis. These systems can identify flaws such as splits, absence of blend, and porosity, allowing prompt corrective actions to be taken. In addition, robotics and automation permit real-time data collection and evaluation, offering instant responses to operators and facilitating quick decision-making procedures.
Additionally, using robotics and automation in fillet weld assessment improves total productivity by reducing evaluation times and raising examination throughput. By improving the assessment process, producers can make sure weld top quality and conformity standards are satisfied effectively, inevitably resulting in cost financial savings and improved item high quality.
Using Artificial Intelligence for Analysis
Artificial knowledge plays a crucial duty in boosting the performance and precision of evaluation in fillet weld assessment procedures. AI formulas can quickly process large amounts of data from weld assessments, discovering flaws or variances that might be challenging to determine with the naked eye.Furthermore, AI systems can pick up from previous evaluation information, continually enhancing their capability to identify see post prospective defects and click for source inconsistencies in fillet welds. This adaptive discovering capability boosts the total top quality control process, reducing the probability of human mistake and guaranteeing that welds meet the called for standards. By incorporating expert system right into fillet weld analysis, sectors can accomplish greater levels of effectiveness, consistency, and conformity in their assessment practices.
Portable Equipment for On-Site Assessment
Enhancing field assessment performance, the adoption of portable devices transforms on-site analysis processes for fillet welds. These devices offer flexibility and benefit, permitting inspectors to carry out detailed examinations in various areas, including remote or tough environments. Mobile tools such as ultrasonic testing tools, magnetic bit assessment tools, and digital radiography systems offer real-time data and high-resolution imaging capacities, enabling fast decision-making and immediate comments on weld top quality.One significant advantage of mobile tools is their capacity to streamline examination procedures, lowering downtime and enhancing total efficiency. Assessors can conveniently transport these tools to various work websites, eliminating the need for delivering heavy equipment or components to off-site facilities. Additionally, the transportability of these tools advertises cost-effectiveness by decreasing transport expenditures and speeding up assessment timelines.
Moreover, the use of mobile devices for on-site assessment advertises aggressive quality assurance actions, as inspectors can promptly identify and attend to any potential welding flaws or disparities. By including these cutting-edge modern technologies right into on-site examination techniques, welding experts can make certain conformity with sector criteria and improve weld top quality, inevitably bring about enhanced architectural stability and safety in various welding applications.
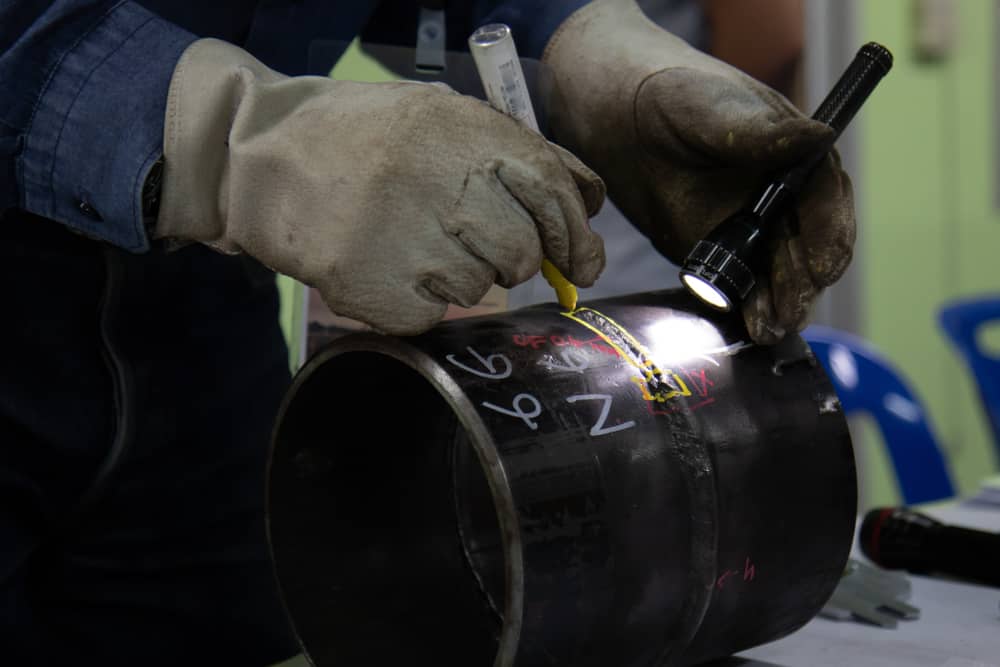
Assimilation of Information Management Systems
Having actually maximized on-site examination procedures with the use of portable tools, the following stage includes the seamless integration of information monitoring systems to further boost efficiency and data evaluation abilities in fillet weld evaluation and testing. By incorporating data management systems into the inspection process, companies can improve information collection, storage space, and analysis. This assimilation allows for real-time monitoring of weld quality, prompt recognition of defects, click reference and timely decision-making to remedy any concerns that may emerge throughout the evaluation procedure.The assimilation of information monitoring systems makes it possible for smooth interaction between different stakeholders involved in the examination procedure, cultivating cooperation and improving general quality control measures. Eventually, the combination of data management systems serves to elevate the criteria of fillet weld assessment and testing, making sure conformity with industry regulations and boosting weld top quality.
Final Thought
In final thought, innovative strategies to fillet weld examination and testing have considerably enhanced weld top quality and compliance standards. Advanced non-destructive screening techniques, robotics, automation, expert system, portable devices, and information monitoring systems have changed the method weld evaluations are performed. By using these technologies, industries can ensure that welds fulfill the required top quality requirements and regulations, eventually improving general efficiency and safety and security in welding procedures.By employing these innovative non-destructive testing strategies, weld inspectors can properly assess the high quality of fillet welds, ensuring conformity with industry requirements and regulations - Welding Inspection Racine. Portable devices such as ultrasonic screening devices, magnetic bit inspection equipment, and electronic radiography systems offer real-time information and high-resolution imaging capabilities, allowing quick decision-making and instant responses on weld quality
Having enhanced on-site evaluation procedures via the utilization of portable devices, the following stage involves the seamless combination of information management systems to additionally boost performance and data analysis abilities in fillet weld examination and testing. Inevitably, the assimilation of information management systems serves to elevate the requirements of fillet weld assessment and screening, ensuring compliance with market laws and improving weld top quality.
In verdict, innovative techniques to fillet weld examination and screening have considerably improved weld high quality and compliance requirements. (Welding Inspection Racine)
Report this wiki page